6 Axis Wheel Force Transducer - 65 kN - 10,5 kNm - Car and SUV
- 3 moment and 3 force measurements in real driving conditions
- Force capacities: Fx, Fz: 65 kN, Fy (lateral): 35 kN
- Moment capacity: 10,5 kNm
- Measures X & Z accelerations
- Signal output : Analog, CAN, optional EtherCAT, Ethernet/IP and CANFD
- Adapts to 12" and larger wheels
- Low cross axis sensitivity
- Environmentally protected
- Temperature compensated
- Rugged stainless steel construction
- Tested to SAE J328 fatigue strength standard
- Swappable slip ring or telemetry system for signal transmission
- ISO-17025 calibration certificate included
- rental option available
Introduction
The LW65 Wheel Force Transducer (WFT) is capable of measuring all of the wheel forces and moments on passenger cars, SUVs, and light duty trucks. It provides independent output signals for vertical, lateral, and longitudinal forces as well as camber, steer, and torque moments. The LW65’s robust, IP67 design is ideal for the harshest track and off-road measurements as well as non-spinning applications to monitor and control laboratory test rigs. For spinning applications, the LW65 offers the convenience of utilizing an outboard slip ring signal transmission or in-board telemetry signal transmission.
Specifications
Maximum Force Capacity, [Fx, Fz] (radial) | 65 kN |
---|---|
[Fy] (lateral) at Tire Patch | 35 kN |
Maximum Torque Capacity [Mx, My, Mz] | 10.5 KNm |
Accelerometer range | 100g |
Sensor | 4 arm strain gage bridges |
Nonlinearity | ≤ 0.2% of full scale output |
Hysteresis | < 0.4% of full scale output |
Cross Axis Sensitivity after correction | < 0.4% of full scale output |
Temperature Range, Operating | -40°C to 125°C |
Angular Resolution | 0.17° |
For use on track, road or test rig
The LW65 Wheel Force Transducer is perfectly wheatherproof and robust, and can be used on road, off-road, snow, mud, stones and trees. The same transducer can be used on test rig as well, ensuring perfect consistency between data measured and tracked and road profiles simulated on dyno.
Installation
The transducer mounts easily on vehicle or test rig (spinning or not spinning) using adapter parts designed for this purpose.
The signal transmission between the transducer and the data acquisition system can be made wired (slip ring option) or wireless (telemetry).
When using an outboard slip ring, the amplifier package easily mounts onto the transducer. It amplifies and digitizes the transducer signals before they pass through the slip ring. The amplifier package also includes X and Z acceleration outputs and performs remote shunt calibration of the transducer. Michigan Scientific Slip Ring Assemblies are known worldwide for their signal quality and robust design.
The measurement signals are processed in real time according the application requirements. CT2 Transducer Interface Box performs real-time coordinate transformation and crosstalk compensation, and provides analog, CAN. EtherCAT signal outputs are also available in option. An embedded webpage allows the user to easily configure the WFT system.
CT2 Transducer Interface Box:
- Performs real-time coordinate transformation and crosstalk compensation
- Easy to use Zero, Shunt Calibration, and Bridge Power Off functions
- Simultaneous Analog, CAN, & Ethernet signal outputs
- Embedded web page enables user to change set-up options, move WFT measurement origin, view transducer static values, create .dbc file
Amplifier and Slip Ring Package
- Internal ± 100 g X & Z accelerometers
- High resolution encoder for position & speed measurement
- Internal smart chip contains all calibration, zero, & shunt values
- Provides signal conditioning & amplification to the transducer strain gage signals
- Digitizes Transducer, Encoder, & Accelerometer signals
- Supports slip ring
Applications
- Driving behaviour assessment (comfort, grip)
- braking tests
- pothole testing
- lane change testing
- vehicle dynamics
- durability testing
- 6axis spinning measurements on test rig
- tire testing
- Application
- Automotive - LD veh.
- Number of Axis
- 6 Axis
- Force Capacity [Fx, Fz]
- 65000 N
- Force Capacity [Fy]
- 35000 N
- Moment capacity
- 10500 Nm
- Nonlinearity (% FS)
- ± 0.2 , 0.4 %
- Hysteresis
- 0.25 % FS
- Analog output signal
- 0-10 VDC
- Tension d'alimentation
- 10 Vcc
- Température de fonctionnement
- -40 to 177 °C
- Rim Size: ≥ 12”
- Special Units for high temperature applications
- Custom designs with alternative output sensitivities / load capacities or dimensions
- durability modification
- EtherCAT output
- Weatherproof Slip Ring
- Encoder / Amplifier (with or without display)
- Adapter parts
Related products
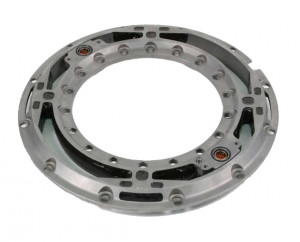