Non contact displacement measurement - extreme conditions - 0.5 to 5 mm
- Operating conditions: < 250 bar and/or 538 °C
- Non-linearity: 1.5 % PE at one temperature
- Bandwidth: 10 kHz (-3dB)
- Measuring range: from 0.9 mm to 5 mm
- 11-point calibration at 3 temperatures
Presentation of the KD8206 1925 or 1950 and 1975
The 1925, 1950 and 1975 sensors are designed for measurements in extreme temperature and/or pressure conditions. These systems are calibrated and built according to precise specifications. The cable and the body of the sensors are made of welded inconel which allows a use from 20 K to 538 °C... The calibration in 3 points of displacement and temperature is realized at the factory at the delivery of the system then adjustable by the user using potentiometers. The 8206 Extreme is supplied with a 19" rack which can be 4, 8 or 12 channels. The KD8206 Extreme has an adjustable analog output of 0-10VDC or 0-5VDC. The sensors are used in research and production. They are used, among other things, to measure thickness or position of metal parts, vibrations, axis centering, out-of-roundness, bearing wear or displacements of vibrating or rotating parts, thus giving the amplitude and frequency of the displacement.
Mounting and measuring principle
Non-contact eddy current displacement sensors are used to measure distances, displacements or positions. They measure the distance between the front face of the sensor and the target which can be magnetic or non-magnetic. This target is necessarily metallic to generate eddy currents: stainless steel, aluminum, copper, steel. The calibration is performed by learning the conditions and the working target.
The KD8206 extreme series has four main advantages:
* Insensitivity to oil, dust, humidity, magnetic fields.
* No physical contact with the target to be measured, there is no movement disturbance and no energy exchange.
* The very high frequency response of the KD8206 (up to 120 KHz).
* The resolution of 1 in 10 000 and the measurement ranges from a few nanometers to several mm.
Applications for extreme sensors 1925-1950 and 1975
Eddy current sensors are used in many applications in research and production. They are used, among other things, to measure thickness or position of metal parts, vibrations, centering of axes, out-of-roundness, wear of bearings or displacements of vibrating or rotating parts giving the amplitude and frequency of the displacement.
* Vibration measurement on rotating parts
* Vibration measurement on non-rotating parts
* Displacement measurement
* Position measurement
PM Instrumentation is the exclusive distributor of KAMAN in France since 1994.
- Technologie
- Eddy Current
- Etendue de mesure linéaire
- 5 mm
- Measuring range
- 0 à ±50 mm
- Nonlinearity (% FS)
- ± 0.25% %
- Bande passante (-3 dB)
- 10000 Hz
- Analog output signal
- 0-5 VDC
- Protection Class
- IP68
- Tension d'alimentation
- 24 Vcc
-
Datasheet_KD-1925_1950_1975_pmi_EN.pdf
-
Datasheet_KD-1925_1950_1975_pmi_FR.pdf
-
Manual-1925-1950-1975-PMI.pdf
-
Kaman_KD-1950_flanged_sensor_IGS.zip
-
Kaman_KD-1950_flanged_sensor_STEP.zip
-
Kaman_KD-1975_flanged_sensor_IGS.zip
-
Kaman_KD-1975_flanged_sensor_STEP.zip
-
Kaman_KD-1925_flanged_sensor_STEP.zip
-
Kaman_KD-1925_flanged_sensor_IGS.zip
-
Kaman_KD-1925_thread_sensor_IGS.zip
-
Kaman_KD-1925_thread_sensor_STEP.zip
See documentation
- Special calibration with non-standard measuring range,
- Temperature compensation of the sensors.
- Special cable; connector on the cable, waterproof feedthrough.
- Treatment of the sensors against moisture.
- Adaptation to a particular target geometry
- Sensor cable length
- 19" rack and table top case
- Data acquisition
- Calibration micrometer
- Teflon thickness gauge
- 12 or 24Vdc continuous power supply
- Product training and calibration technique
Related products
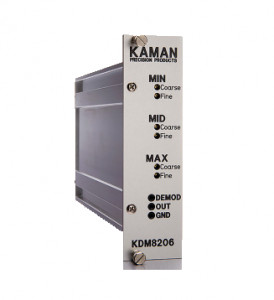
KD8206 - Multivoies - 50 kHz
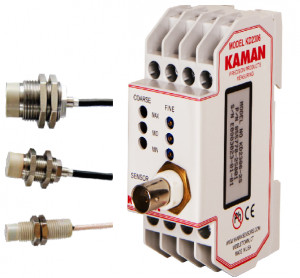