Fatigue Force Transducer | ±1250 N to ±4500 kN | Tension Compression
- Fatigue force measurement
- Number of cycles: 100 million at full load
- Measurement range: ±1.25 kN to ±4500 kN
- Accuracy: ±0.05% to ±0.1% of full scale depending on the model
- Insensitive to transverse forces
- Low deflection
- Tension / compression measurement
- Overload protection: 300%
- Output signal: 1 to 2 mV/V
- Operating temperature: -55 to 90°C
- Double or triple bridges optional
Presentation
High Capacity High Performance Fatigue Sensor
The 1000 series are high-precision tension/compression fatigue force transducers designed for endurance test benches, fatigue test benches, or any other mechanical lifetime test equipment. The measurement ranges are between ±1.25 kN and ±4.5 MN. These sensors are qualified for fatigue testing up to 100 million cycles at 100% of the nominal load.
Design
The design of the 1000 series sensors is the result of 50 years of continuous improvement. The choice of strain gauges, construction, manufacturing expertise, and calibration techniques enable a precision of ± 0.03% of full scale, with excellent repeatability (< 0.02%) and long-term stability (static accuracy: 0.04%). The construction is almost insensitive to eccentric (< 0.05% / cm) and transverse forces (< 0.01%), and is extremely robust, with overload protection up to 300%.
The operating temperature range is from -55 to 90°C, and calibration is temperature-compensated between -10 and 45°C.
Specifications
- Measurement: Tension / Compression
- Bridge supply: 1-20 VDC
- Bridge resistance: 350 Ohm
- Overload protection: 300%
Model (plan) | Measurement Ranges | Non-linearity | Hysteresis | Deflection | Output | Weight |
---|---|---|---|---|---|---|
1010 | ±1.25 / ±2.5 / ±5 kN | ± 0.04% | ± 0.04% | 0.013 mm | 1.0 mV/V | 0.7 kg |
1010 | ±12.5 / ±25 kN | ± 0.04% | ±0.04% | 0.013 mm | 1.0 mV/V | 0.7 kg |
1020 | ±50 / ±125 kN | ±0.04% | ±0.04% | 0.025 mm | 2.0 mV/V | 4.3 kg |
1032 | ±225 kN | ±0.04% | ±0.04% | 0.050 mm | 2.0 mV/V | 12 kg |
1040 | ±450 kN | ±0.06% | ±0.06% | 0.08 mm | 2.0 mV/V | 68 kg |
1044 | ±600 kN | ±0.08% | ±0.08% | 0.08 mm | 2.0 mV/V | 70 kg |
1052 | ±900 kN | ±0.09% | ±0.09% | 0.10 mm | 2.0 mV/V | 100 kg |
1060 | ±1500 kN | ±0.10% | ±0.10% | 0.10 mm | 2.0 mV/V | 200 kg |
1080 | ±2250 kN | ±0.15% | ±0.15% | 0.13 mm | 2.0 mV/V | 450 kg |
1090 | ±4500 kN | ±0.20% | ±0.20% | 0.13 mm | 2.0 mV/V | 860 kg |
Installation
- Bridge supply: 1-20 VDC
- Mounting 1: Tension only. The load is applied via a ball joint + nut. Sensor installation with base when the installation surface has imperfections (see accessories). Types of screws, tightening torques here
- Mounting 2: Tension/compression. The load is applied via a threaded rod + nut. Sensor installed directly on the surface. Types of screws, tightening torques here
- Mounting 3: Tension/compression, in-line, with bases and ball joints on both sides of the sensor. Types of screws, tightening torques here
Detailed mounting instructions here
Signal Conditioning and Acquisition
The output signal from the 1000 series sensors is unamplified. A complete measurement chain, wired and configured specifically for the application, can be obtained by integrating a Display, an Analog conditioner/amplifier with voltage or current output, or a PC or PLC acquisition system with included acquisition software. For more information, please contact us.
Applications
- Fatigue test benches in aerospace, automotive industries
- Rupture testing
- Endurance test bench instrumentation
- Hydraulic cylinder instrumentation
- Breaking strength of massive parts
Options and Accessories
- Type
- pancake
- Precision (max error)
- ≤ 0.1 %
- Nonlinearity (% FS)
- ± 0.03 , 0.05 %
- Hysteresis
- 0.03 % FS
- Nonrepeatability
- 0.02 % FS
- Temperature Compensated Range
- -10 to 45 °C
- Température de fonctionnement
- -55 to 90 °C
- Zero Balance
- 0.0015 %PE/°C
- Sensibilité du gain
- 0.0015 %/°C
- Analog output signal
- non-amplifié
- Output Signal
- 2 , 1 mV/V
- Résistance du pont
- 350 Ω
- Tension d'alimentation
- 10 Vcc
- Measurement direction
- Traction & Compress.
- Surcharge
- 300 %PE
- Housing
- Steel
- Protection Class
- IP40
- Measuring Range (Force)
- 1 - 100 kN, 100 - 250 kN, > 250 kN, > 1 MN
- Application
- High Accuracy, Durability
-
Datasheet_1000_pmi_EN-%282%29.pdf
-
CalAdaptor-1.pdf
-
Datasheet_1000_pmi_FR.pdf
-
Installation-Low-Profile.pdf
-
1X10-Drawing.pdf
-
1X20-Drawing.pdf
-
1X32-Drawing.pdf
-
1X40-Drawing.pdf
-
1X44-Drawing.pdf
-
1X52-Drawing.pdf
-
1X60-Drawing.pdf
-
1080-1280.pdf
-
1090-Drawing.pdf
-
Interface-1010-250-thru--5K-B.STEP
-
Interface-1010-1.25KN-thru--25KN-B.STEP
-
Interface-1020-12.5K-B.STEP
-
Interface-1020-25K-B.STEP
-
Interface-1020-50KN-B.STP
-
Interface-1020-125KN.STEP
-
Interface-1020-125KN-B.STEP
-
Interface-1032-50K-B.STEP
-
Interface-1032-225KN-B.STEP
Dimensions 1010, 1020, 1032
Dimensions 1040 à 1090
Connectique
Options
Connectors
Bayonet Connector | Screw Connector | 3m Cable Output |
---|---|---|
![]() |
![]() |
![]() |
PT02E-10-6P Connector / Option ACK or CDS | PC04E-10-6P Connector / Option AF or ALD | Option AJ |
Redundant Strain Gauge Bridge
Double or triple
TEDS
According to standard
Calibration
ISO 17025 or E74 NIST
Base
1210 | 1210 | 1220 | 1232 | 1240 | 1244 | 1252 | 1260 | 1280 | 1290 |
---|---|---|---|---|---|---|---|---|---|
B101(M) | B102(M) | B103(M) | B112(M) | B105(M) | B116(M) | B121(M) | B122(M) | B123(M) | B125(M) |
Precision Threaded Rod
Ball Joints
Accessories
Display
Visualizes the measurement in units, manages alarms, and displays max-min values.
Conditioner
Output ±5VDC, ±10 Vcc, 0-10 Vcc or 4-20 mA.
Acquisition Systems
Transmits measurement signals to a PC, programmable logic controller, recorder, or SCADA-type supervision application. Post-processing of measurement data via Excel or Matlab.
Related products
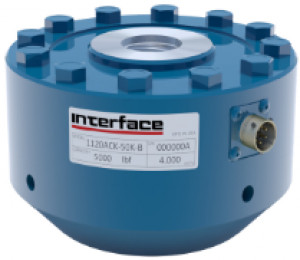
1100 Série - Haute précision
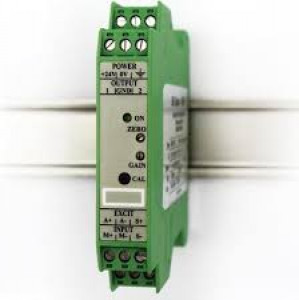
PMI 520 AJ
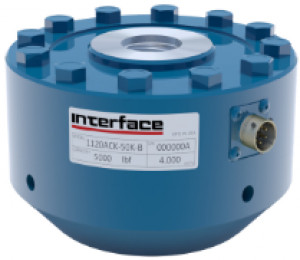