6 axis force/torque transducer - 1kN/200Nm to 15kN/1,2kNm
- type: 6-axis force- torque sensor;
- measuring ranges: 1kN/200Nm, 5kN/500Nm, 15kN/1.2kNm;
- accuracy class: 0.2%;
- dimensions: Ø130 mm x 80 mm;
- mounting and centering: 6 x female thread M12x1.75; 2 drill hole Ø8 mm E7;
- connection: cable gland (CG) 5m 30-24 PUR/24x0,06 mm2 / integrated round plug connector (M16)/ integrated round plug connector (MP11);
- material: aluminium alloy / stainless steel;
- weight: 1500 g / 3200 g;
Introduction
The 6-component load cell K6D130 simultaneously measures the forces Fx, Fy, Fz and torques Mx, My, Mz on three perpendicular axes. This "second generation" 6-component sensor integrates 6 independent strain gauge force sensors. The forces are measured directly at the contact surface, allowing maximum rigidity and a reduced size. The contact surfaces are designed for optimized force transmission, reducing non-repeatability to about 0.1%, overall accuracy to 0.2% (after decoupling), and crosstalk sensitivity to 1%.
The K6D130 sensor is available in 3 measuring ranges:
Model | K6D130 (1kN/200Nm) | K6D130 (5kN/500Nm) | K6D130 (15kN/1,2kNm) |
---|---|---|---|
Fx, Fy [kN] | 1 | 5 | 15 |
Fz [kN] | 2,5 | 15 | 50 |
Mx, My, Mz [Nm] | 200 | 500 | 1200 |
Connectic | Connector : MP11 Câble : CG | Connector : MP11 ou M16 Cable : CG | Connector : MP11 ou M16 Cable : CG |
Material | Aluminium | Aluminium | High strength stainless steel 1.4542 |
Calibration
Each transducer is delivered with a factory calibration certificate, as well as a 6x6 channel coupling matrix, identified in calibration to minimize cross-talks.
The real forces are obtained by multiplying the 6x6 decoupling matrix (M) by the vector I containing the 6 output signals of the K6D130. The origin of the reference frame in which the measured forces are projected is generally the center of the contact surface (see documentation). After neutralization of the inter-channel effects, a force applied on one axis will result in a force variation on only one axis. The accuracy of the measurement is thus improved by a factor of 5 to 10.
Calibration to specific measuring ranges is available as an option, as well as ISO-17025 calibration.
Installation
The 6-component load cell K6D130 is easily installed on machine tools, arms, or test benches. The introduction of the forces and the fixing to the bench are carried out by 6 taps M12 x 1.75 of 15mm of depth + 2 pins of contrage Ø8 mm E7 (Torques of tightenings: see here).
The application of the force is made on the portions of the surface raised by 1 mm. The inner part of the surface is used for centering.
The operating temperature range is -10 to 85°C.
Measuring chain
A complete measurement chain for the supply, visualization and acquisition of measurement signals is configured according to the specific needs of the application.
Connectivity
A connector, detachable or not, is systematically proposed with the 6 axis sensor. The length, standard 5m, is specifiable. The output connector is specifiable.
Acquisition module and software
K6D sensors are usually delivered with a GSV-8DS electronics and GSVmulti acquisition software. Main features:
- 8 universal analog channels (gauge, thermocouple, +/- 10V, etc...)
- sampling : 48 kHz
- Real time application of the inter-channel decoupling matrix
- Interface: USB, RS-232, optional: CAN, WiFi, EtherCAT, LAN, LTE, Blutooth...
- Visualization and acquisition software Windows 7, 10
Dll and VI files are also provided for the development of an application under Labview or in C / Visual Studio / C++ / .net
Application
The multi-component force sensor is very well suited for use in robotics, e.g.
- For collision detection
- "Teach-In" Collision detection
- Force or torque-controlled operation
- Load measurement in medicine, prosthetics, orthopaedic engineering
- Measurement in sports medicine
- Comfort / ergonomics measurements
Options and accessories
- Calibration: Standard or [specific] (https://www.pm-instrumentation.com/storage/3892/Calibration-option-Matrix-Plus.pdf), ISO-17025
- Robotic mounting kit (ISO 9409 standard)
- Cable and connector for GSV
- Packaging and acquisition module GSV-8DS, GSV-8AS or GSV-6LTE
- Extended temperature compensation
- TEDS
- Type
- 6 axis sensor
- Number of Axis
- 6 Axis
- Precision (max error)
- ≤ 0.1 %
- Nonlinearity (% FS)
- ± 0.1 %
- Tension d'alimentation
- 10 Vcc
- Measurement direction
- Traction & Compress.
- Housing
- Aluminium
- Protection Class
- IP65
- Measuring Range (Force)
- 1 - 100 kN, 100 - 250 kN
- Application
- Robotics
- Calibration: Standard or specific, ISO-17025
- Cable and connector for GSV
- Extended temperature compensation
- TEDS
Related products
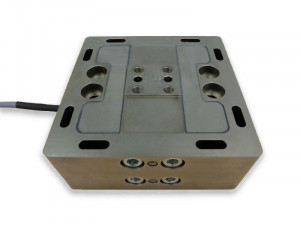
K3D160 - 3 axes - IP67 - 2 kN à 50 kN
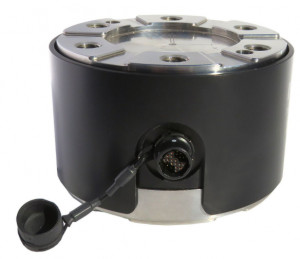