Force & Torque Sensor – Fz 5 kN / Mx-My 100 Nm – Ø110 – IP66
- 3-Axis Force & Torque Sensor
- Measurement range – Fz: ±50 N, ±100 N, ±200 N, ±500 N, ±1 kN, ±2 kN, ±5 kN
- Measurement range – Mx/My: ±1 Nm, ±2 Nm, ±4 Nm, ±10 Nm, ±20 Nm, ±40 Nm, ±100 Nm
- Accuracy: 0.1%
- Output signal: 1 mV/V
- Dimensions: Ø110 mm × 14 mm / Ø110 mm × 20 mm
- Center bore: 25 mm H7
- Mounting: 8 threaded holes M6 on Ø50 mm and Ø100 mm bolt circles
- Material: Aluminum / Stainless Steel
- Calibration: Tension and Compression
- Connection: 10-wire cable, 3 m length, PUR 24-10
Overview
The K3R110 3-component sensor is a simple, precise, and cost-effective solution for simultaneous measurement of axial force (Fz) and torques (Mx/My) in a compact format (thickness: 14 to 20 mm).
The K3R110 sensor features an outer ring (fixed to the structure) and an inner ring (connected to the sample), linked by four instrumented beams, each equipped with a full strain gauge bridge. A central 25 mm diameter bore allows for the passage of a shaft, electrical wiring, or hydraulic connections.
The K3R110 can also be used as a 3-axis force sensor (Fx/Fy/Fz) by converting torque values into forces, using the known distance between the sensor's center and the point of force application.
Specifications
Eight versions are available, with force ranges from ±50 N to ±5 kN, and torque ranges from ±1 Nm to ±100 Nm. Accuracy is 0.1%.
Model | Fz [N] | Mx, My [Nm] | Material | Drawing |
---|---|---|---|---|
K3R110_50N_1Nm | 50 | 1 | Aluminum | Drawing |
K3R110_100N_2Nm | 100 | 2 | Aluminum | Drawing |
K3R110_200N_4Nm | 200 | 4 | Aluminum | Drawing |
K3R110_200N_4Nm_VA | 200 | 4 | Stainless steel | Drawing |
K3R110_500N_10Nm_VA | 500 | 10 | Stainless steel | Drawing |
K3R110_1000N_20Nm_VA | 1000 | 20 | Stainless steel | Drawing |
K3R110_2000N_40Nm_VA | 2000 | 40 | Stainless steel | Drawing |
K3R110_5000N_100Nm_VA | 5000 | 100 | Stainless steel | Drawing |
Models with ranges of 50N/1Nm, 100N/2Nm, and 200N/4Nm are made of aluminum alloy. Higher-capacity models are made of high-strength stainless steel (1.4542).
Installation
The K3R110 3-component force sensor is easy to install on machine tools, robotic arms, or test benches. Load application and sensor fixation are ensured via two sets of 4x M6 threaded holes (bolt circles: 50 mm and 100 mm) and 4x Ø6.5 mm alignment dowel holes.
- Supply voltage: 5 VDC
- Operating temperature range: -10°C to +85°C
- Output signal: non-amplified
- Supplied with 3-meter 10-wire cable (PUR 24-10)
Signal Conditioning, Acquisition, and Decoupling Matrix Use
The output vector L [Fz; Mx; My] is calculated by applying a decoupling matrix A to the four raw output signals U from the K3R110. This 12-term matrix A is specific to each sensor and identified during calibration.
A | Ch 1 | Ch 2 | Ch 3 | Ch 4 |
---|---|---|---|---|
Fz | a11 [N/mV/V] | a12 [N/mV/V] | a13 [N/mV/V] | a14 [N/mV/V] |
Mx | a21 [Nm/mV/V] | a22 [Nm/mV/V] | a23 [Nm/mV/V] | a24 [Nm/mV/V] |
My | a31 [Nm/mV/V] | a32 [Nm/mV/V] | a33 [Nm/mV/V] | a34 [Nm/mV/V] |
Recommended Modules
- GSV-8DS – High-performance 8-channel signal conditioner
- GSV-8AS – Rugged version
- GSV-4USB – 4-channel USB strain gauge conditioner
The included GSV-multi software supports real-time application of the decoupling matrix A, enabling direct acquisition of real force and torque values.
Applications
- Robotics
- Manufacturing
- Quality control
- Load measurement in medical devices, prosthetics, orthopedics, or gait analysis
- Sports science
- Ergonomics and comfort testing
- Type
- beam sensor
- Number of Axis
- 3 Axis
- Precision (max error)
- ≤ 0.1 %
- Température de fonctionnement
- -10 to 85 °C
- Analog output signal
- non-amplifié
- Résistance du pont
- 350 Ω
- Tension d'alimentation
- 10 Vcc
- Measurement direction
- Traction & Compress.
- Déflection
- 0.1 mm
- Surcharge
- 150 %PE
- Protection Class
- IP66
- Measuring Range (Force)
- 1 - 100 kN
- Transducer Series
- K3R
- Application
- High Accuracy, OEM, low cost
- Connector on cable for acquisition
- Extended temperature compensation
- Signal conditioning and acquisition electronics
- Connector output available on request
- TEDS module
- Bouton de charge
- Electronique de conditionnement
- Afficheur
- Câblage spécifique
Related products
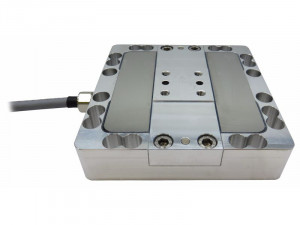
K3D120 - 3 axes - IP66 - 50 N à 5 kN
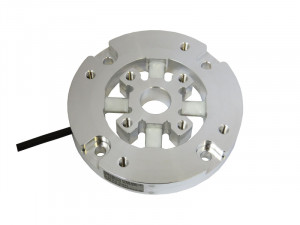
K3R70 - Fz+Mxy - Ø70 - 100N - 1Nm
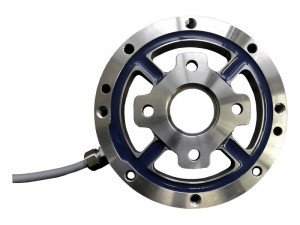