6-axis force transducer - 50N/5Nm up to 500N/20Nm
- 6 components force+torque transducer - série F6D/K6D
- Measuring ranges: 50N/5Nm, 200N/5Nm, 500N/20Nm
- Accuracy class: 0.2%;
- Output signal: analog, USB, EtherCAT, WiFi (optional amplifier)
- Dimensions: Ø 60 mm x 40 mm;
- Mounting and centring: 6 x M5x0.8 + 2 centring pins Ø3 mm E7
- Connection: MP11 24 pin male connector
- IP65 construction Aluminium/stainless steel or all stainless steel depending on version
- Weight: 160 to 450 g
- Calibration certificate and 6x6 channel matrix included
Overview
The 6-component force transducer K6D40 is designed to measure the forces Fx/Fy/Fz and the 3 moments Mx/My/Mz over ranges up to Fxy: 500N / Fz: 2000N / Mxy: 20Nm / Mz: 40 Nm. The "3D force/torque" sensor has an extremely small footprint, with a diameter of only 60 mm.
The transducer is equipped with 24 miniature high resistance strain gauges of the latest generation forming 6 complete bridges. Despite its small size, the 6-component K6D40 load cell is very robust: IP65 aluminum/stainless steel housing, temperature-resistant yet flexible Teflon cable, and particularly suitable for medical technology applications. The overall accuracy is 0.2% (after decoupling), the crosstalk sensitivity is 1%, and the sensor has a very good frequency response due to its high rigidity.
Specifications
Model | K6D40 (50N/5Nm/CG) | K6D40 (50N/5Nm/MP11) | K6D40 (200N/5Nm/CG) | K6D40 (200N/5Nm/MP11) | K6D40 (500N/20Nm/CG) | K6D40 (500N/20Nm/MP11) |
---|---|---|---|---|---|---|
Fx [N] | 50,00 | 50,00 | 200,00 | 200,00 | 500,00 | 500,00 |
Fy [N] | 50,00 | 50,00 | 200,00 | 200,00 | 500,00 | 500,00 |
Fz [N] | 200,00 | 200,00 | 500,00 | 500,00 | 2000,00 | 2000,00 |
Mx [Nm] | 5,00 | 5,00 | 5,00 | 5,00 | 20,00 | 20,00 |
My [Nm] | 5,00 | 5,00 | 5,00 | 5,00 | 20,00 | 20,00 |
Mz [Nm] | 10,00 | 10,00 | 10,00 | 10,00 | 40,00 | 40,00 |
Connectique | Cable | Connecteur MP11 | Cable | Connecteur MP11 | Cable | Connecteur MP11 |
Calibration
Each sensor is delivered with a factory calibration certificate, as well as a 6x6 cross-talk matrix, identified in calibration to minimise cross-talk
The real forces are obtained by multiplying the 6x6 decoupling matrix (M) by the vector I containing the 6 output signals of the K6D40. The origin of the reference frame in which the measured forces are projected is usually the centre of the contact surface (see documentation). After neutralising the effects of the channels, a force applied on one axis will result in a force variation on only one axis. The accuracy of the measurement is thus improved by a factor of 5 to 10.
Calibration to specific measuring ranges is available as an option, as well as ISO-17025 calibration.
Installation
The two mounting flanges are symmetrical. Each has a Ø47mm centring contour and a Ø3mm centring pin. The force is introduced and fixed to the bench by 6 x M6 x 0.8 threads + the 2 Ø3 mm E7 centring pins (tightening torques: see here). The application of force is carried out on the surface portions raised by 1 mm.
The operating temperature range is -10 to 85°C.
Measuring chain
A complete measurement chain for the supply, visualisation and acquisition of measurement signals is configured according to the specific needs of the application.
Connection system
A cable is systematically offered with the 6-axis sensor. The length, standard 5m, can be modified on demand. The output connector can be specified.
Acquisition module and software
K6D sensors are usually delivered with GSV-8DS electronics and GSVmulti acquisition software. Main features:
- 8 universal analogue channels (gauge, thermocouple, +/- 10V, etc...)
- Sampling: 48 kHz
- Real time application of the inter-channel decoupling matrix
- Interface: USB, RS-232, optional: CAN, WiFi, EtherCAT, LAN, LTE, Bluetooth...
- Visualisation and acquisition software Windows 7, 10
Dll and VI files are also provided for application development in Labview or C / Visual Studio / C++ / .net
Applications :
The application areas of the K6D40 sensor are for example:
- Static and dynamic testing
- Material testing
- Strength of materials testing
- Hexapod testing
- Static and dynamic force in wind tunnels
- Stress measurement in medical technology / prosthetics / orthopaedic technology / gait analysis
- Robotics: collision detection
- Measurements in sports medicine
- Comfort measurements / ergonomic measurements
- Monitoring of assembly processes
- Type
- 6 axis sensor
- Moment capacity
- 5 / 20 Nm
- Number of Axis
- 6 Axis
- Precision (max error)
- 0.5 %
- Nonlinearity (% FS)
- ± 0.1 %
- Hysteresis
- 0.1 % FS
- Nonrepeatability
- 0.5 % FS
- Zero Balance
- 0.1 %PE/°C
- Sensibilité du gain
- 0.05 %/°C
- Output Signal
- 0.4 mV/V
- Tension d'alimentation
- 10 Vcc
- Measurement direction
- Traction & Compress.
- Housing
- Steel
- Protection Class
- IP42
- Measuring Range (Force)
- ⩽ 1 kN
- Application
- OEM, Robotics, Miniature
Connector Version
Options et accessoires
- Calibration: Standard ou spécifique, ISO-17025
- Câble et connectique pour GSV
- Module de conditionnement et d'acquisition GSV-8DS, GSV-8AS ou GSV-6LTE
- Compensation en température étendue
- TEDS
- Bouton de charge
- Electronique de conditionnement
- Afficheur
- Câblage spécifique
Related products
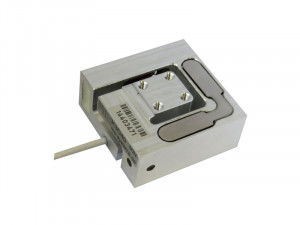