6 axis force transducer | Fz : 2 to 20 kN - Mz : 20 to 500 Nm
- 6-component force/torque sensor of the F6D/K6D series
- Measuring ranges: Fz : 2 to 20 kN - Mz : 20 to 500 Nm
- Accuracy class: 0.2%;
- Output signal: not amplified
- Dimensions: Ø83 mm x 64 mm;
- Mounting and centering: 6 x M10x1.5 threads + 2 centering pins Ø6 mm H7
- Connection: 5 m cable 33-24 PUR/24x0,03 mm2 (CG);
- IP65 construction in aluminum or stainless steel according to models
- Weight: 830 to 1050 g depending on model
- Calibration certificate and 6x6 inter-channel matrix supplied
Introduction
The 6-component force transducer K6D68 is ideal for applications with space constraints. It simultaneously measures the forces Fx, Fy, Fz and torques Mx, My, Mz on three perpendicular axes with a measurement accuracy of 0.2 % of full scale (after application of the inter-channel matrix). The forces are measured directly at the contact surface, allowing maximum rigidity and a small footprint. It is ideally suited for robotics, wind tunnel applications or any type of application where all 6 force components are measured accurately.
The K6D68 sensor is available in 5 measuring ranges :
K6D68 | (1kN/20Nm) | (2kN/50Nm) | (5kN/50Nm) | (10kN/100Nm) | (10kN/500Nm) |
---|---|---|---|---|---|
Fx, Fy [kN] | 1000 | 2000 | 5000 | 10000 | 10000 |
Fz [kN] | 2000 | 4000 | 10000 | 20000 | 20000 |
Mx, My, Mz [Nm] | 20 | 50 | 50 | 100 | 500 |
Material | Aluminium | Aluminium | Acier | Acier | Acier |
Documentation page | 3-4 | 5-6 | 7-8 | 9-10 | 11-12 |
Each transducer is delivered with a factory calibration certificate and a 6x6 inter-channel coupling matrix. Calibration to specific ranges is available as an option, as well as ISO-17025 calibration.
Installation
The 6-component load cell K6D68 is easily installed on machine tools, arms, or test benches. The introduction of the forces and the fixing to the bench are carried out by 6 tappings M10x1.5 + 2 pins of contrage Ø6 mm H7 (Torques of tightening: see here). The application of force is carried out on the portions of the surface raised by 1 mm. The inner part of the surface is used for centering.
The sensor is supplied with 5 VDC. The operating temperature range is -10 to 85°C. The output signal is not amplified. The sensor is delivered with a 5m cable.
Conditioning, Acquisition, Use of the decoupling matrix
The acquisition of the raw measurement signals can be done with :
- a PC or PLC acquisition system equipped with a strain gage bridge input card
- or via a conditioning module for strain gage bridge with analog or digital output, then a PC or a standard acquisition system.
The inter-channel decoupling matrix is implemented in the conditioning or acquisition module.
The real forces are obtained by multiplying the 6x6 decoupling matrix (M) by the vector I containing the 6 output signals of the K6D68. The origin of the reference frame in which the measured forces are projected is generally the center of the contact surface (see documentation). After neutralization of the inter-channel effects, a force applied on one axis will result in a force variation on only one axis. The accuracy of the measurement is thus improved by a factor of 5 to 10.
PM Instrumentation recommends the GSV series of digital interface conditioning modules for their simplicity of use, their accuracy and their ability to take into account decoupling matrices:
- the GSV-8DS (High performance module, 8 analog inputs) or its ruggedized version GSV-8AS, which can be optionally equipped with a datalogger
- the GSV-6BT, miniature wireless conditioner
- the GSV-6LTE, equipped with a datalogger and wireless connectivity.
A visualization and acquisition software is included with these modules (GSV-multi). Dll and VI files are also provided for application development under Labview or in C / Visual Studio / C++ / .net
Applications
The 6-component force sensor K6D68 is suitable for a wide range of applications in robotics, production, material or medical studies such as:
- Collision detection
- Teach-in or presence detection
- Force or torque controlled operation
- Stress measurement in medical technology
- Strength of materials testing
- Gripping in robotics
- Orthopedic technology
- Gait analysis measurements in sports medicine Comfort measurements
- ergonomic measurements
- Assembly process monitoring
- Control of machining in effort
Options and accessories
- Calibration: Standard or [specific] (https://www.pm-instrumentation.com/storage/3892/Calibration-option-Matrix-Plus.pdf), ISO-17025
- Robotic mounting kit (ISO 9409 standard)
- Cable and connector for GSV
- Packaging and acquisition module GSV-8DS, GSV-8AS, GSV-6BT or GSV-6LTE
- Extended temperature compensation
- TEDS
- Type
- 6 axis sensor
- Measuring Range
- 2000 , 4000 , 10000 , 20000
- Moment capacity
- 20 / 50 / 100 / 500 Nm
- Number of Axis
- 6 Axis
- Precision (max error)
- 0.25 %
- Nonlinearity (% FS)
- ± 0.1 %
- Hysteresis
- 0.1 % FS
- 1 % PE
- Temperature Compensated Range
- -10 to 70 °C
- Température de fonctionnement
- -10 to 85 °C
- Analog output signal
- non-amplifié
- Output Signal
- 0.4 mV/V
- Résistance du pont
- 350 Ω
- Tension d'alimentation
- 10 Vcc
- Measurement direction
- Traction & Compress.
- Surcharge
- 150 %PE
- Protection Class
- IP65
- Measuring Range (Force)
- 1 - 100 kN, 100 - 250 kN
- Application
- OEM, Robotics
- Connections
- Extended temperature compensation
- High precision calibration
- TEDS module
- Calibration: Standard or [specific] (https://www.pm-instrumentation.com/storage/3892/Calibration-option-Matrix-Plus.pdf), ISO-17025
- Robotic mounting kit (ISO 9409 standard)
- Cable and connector for GSV
- Packaging and acquisition module GSV-8DS, GSV-8AS, GSV-6BT or GSV-6LTE
Related products
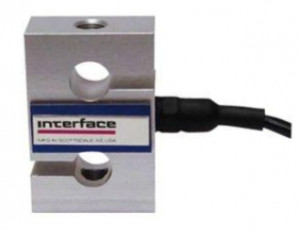