Sensor 3 forces + 3 torques - 500N to 5kN - 20 to 500 Nm
- 6-component force/torque sensor of the F6D/K6D series
- Force measurement ranges: 0.5 kN to 5 kN
- Torque measuring range: 20 to 250 Nm
- Accuracy class: 0.2%;
- Output signal: not amplified
- Dimensions: Ø 80 mm x 50 mm;
- Calibration: Tension and compression
- Mounting and centering: 6 x M5x0,8 + 2 centering pins Ø3 mm E7
- Connection: cable gland (CG) with 5 m cable 33-24 PUR/24x0,03 mm2 OR MP11 24 pins male connector
- IP65 construction Aluminium/stainless steel or all stainless steel depending on version
- Weight: 450g to 1kg depending on version
- Calibration certificate and 6x6 inter-channel matrix supplied
Introduction
The multi-component sensor K6D80 allows to measure forces Fx/Fy/Fz and moments Mx/my/Mz on three perpendicular axes simultaneously, in a reduced size (diameter: 80mm, height: 50mm). 7 versions are available, with force measurement ranges from 500N to 5kN, and torque measurement ranges from 20Nm to 250Nm.
Specifications
Model | Fx, Fy [N] | Fz [N] | Mx, My, Mz [Nm] | Connectivity |
---|---|---|---|---|
K6D80_500N_20Nm_MP11 | 500,00 | 1000,00 | 20,00 | Connector MP11 |
K6D80_1kN_50Nm_CG | 1000,00 | 2500,00 | 50,00 | Cable |
K6D80_1kN_50Nm_MP11 | 1000,00 | 2500,00 | 50,00 | Connector MP11 |
K6D80_2kN_100Nm_CG | 2000,00 | 5000,00 | 100,00 | Cable |
K6D80_2kN_100Nm_MP11 | 2000,00 | 5000,00 | 100,00 | Connector MP11 |
K6D80_5kN_250Nm_CG | 5000,00 | 15000,00 | 250,00 | Cable |
K6D80_5kN_250Nm_MP11 | 5000,00 | 15000,00 | 250,00 | Connector MP11 |
This 6-component load cell uses a rod construction that absorbs forces and torques directly on the pitch circle of the fastening wire, increasing stiffness and extending torque capacity.
The force transmission is applied to ring-shaped segments raised by 1 mm on the upper side, ensuring an even distribution of forces and optimized repeatability (repeatability error < 0.1%). The inside diameter of the segments is used for centering.
The K6D80 2kN / 100Nm load cell is made of aluminum alloy, the K6D80 5kN / 250Nm load cell is made of high strength stainless steel 1.4542.
Installation
The 6-component load cell K6D80 is easily installed on machine tools, arms, or test benches. The introduction of the forces and the fixing to the bench are carried out by 6 tappings M5x0,8 + 2 centering pins Ø3 mm E7 (Tightening torques: see here). The application of force is carried out on the portions of the surface raised by 1 mm. The inner part of the surface is used for centering.
The sensor is supplied with 5 VDC. The operating temperature range is -10 to 85°C. The output signal is not amplified. The sensor is delivered with either a connector or a 5m cable.
Conditioning, Acquisition, Use of the decoupling matrix
The acquisition of the raw measurement signals is done with
- a PC or PLC acquisition system equipped with a strain gage bridge input card
- or via a strain gage bridge conditioning module with analog or digital output, then a PC or a standard acquisition system.
The inter-channel decoupling matrix is implemented in the conditioning or acquisition module.
The real forces are obtained by multiplying the 6x6 decoupling matrix (M) by the vector I containing the 6 output signals of the K6D80. The origin of the reference frame in which the measured forces are projected is generally the center of the contact surface (see documentation). After neutralization of the inter-channel effects, a force applied on one axis will result in a force variation on only one axis. The accuracy of the measurement is thus improved by a factor of 5 to 10.
PM Instrumentation recommends the GSV series of digital interface conditioning modules for their simplicity of use, their accuracy and their ability to take into account decoupling matrices:
- the GSV-8DS (High performance module, 8 analog inputs) or its ruggedized version GSV-8AS, which can be optionally equipped with a datalogger
- the GSV-6LTE, equipped with a data logger and wireless connectivity A visualization and acquisition software is included with these modules (GSV-multi). Dll and VI files are also provided for the development of an application under Labview or in C / Visual Studio / C++ / .net
Applications
Robotics
- Detection of collisions during the learning phase ("Teach" function)
- Presence detection and error detection
- Force or torque controlled operation
Medicine
- Load measurement in medicine, prosthetics, orthopedic engineering or gait analysis
- Measurement in sports medicine
- Comfort / ergonomics measurements
Options and accessories
- Calibration: Standard or [specific] (https://www.pm-instrumentation.com/storage/3892/Calibration-option-Matrix-Plus.pdf), ISO-17025
- Robotic mounting kit (ISO 9409 standard)
- Cable and connector for GSV
- Packaging and acquisition module GSV-8DS, GSV-8AS or GSV-6LTE
- Extended temperature compensation
- TEDS
- Type
- 6 axis sensor
- Moment capacity
- 20 / 250 / 50 / 100 Nm
- Number of Axis
- 6 Axis
- Precision (max error)
- 0.5 %
- Tension d'alimentation
- 10 Vcc
- Measurement direction
- Traction & Compress.
- Housing
- Steel
- Protection Class
- IP42
- Measuring Range (Force)
- ⩽ 1 kN, 1 - 100 kN
- Application
- High Accuracy, Robotics
80 mm x 50 mm
- Calibration: Standard or [specific] (https://www.pm-instrumentation.com/storage/3892/Calibration-option-Matrix-Plus.pdf), ISO-17025
- Robotic mounting kit (ISO 9409 standard)
- Cable and connector for GSV
- Packaging and acquisition module GSV-8DS, GSV-8AS or GSV-6LTE
- Extended temperature compensation
- TEDS
- Calibration: Standard or [specific] (https://www.pm-instrumentation.com/storage/3892/Calibration-option-Matrix-Plus.pdf), ISO-17025
- Robotic mounting kit (ISO 9409 standard)
- Cable and connector for GSV
- Packaging and acquisition module GSV-8DS, GSV-8AS or GSV-6LTE
- Extended temperature compensation
- TEDS
Related products
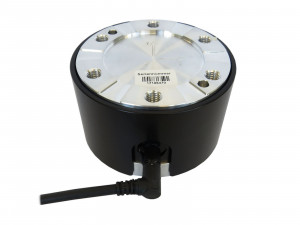
K6D130 - 6 axes - Ø130 x 80 mm
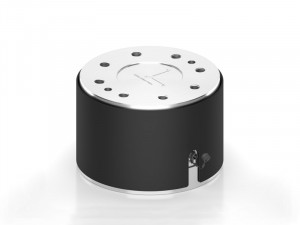